Technologie tavení
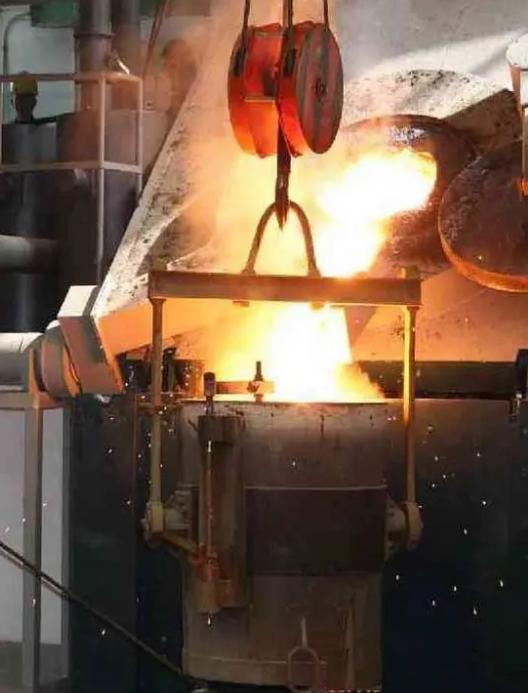
V současné době tavení produktů zpracování mědi obecně přijímá indukční tavicí pec a také přijímá tavení v dozvukové peci a tavení v šachtové peci.
Tavení v indukční peci je vhodné pro všechny druhy mědi a slitin mědi a má vlastnosti čistého tavení a zajištění kvality taveniny.Podle konstrukce pece se indukční pece dělí na jádrové indukční pece a bezjádrové indukční pece.Indukční pec s jádrem se vyznačuje vysokou účinností výroby a vysokou tepelnou účinností a je vhodná pro kontinuální tavení jedné řady mědi a slitin mědi, jako je červená měď a mosaz.Indukční pec bez jádra se vyznačuje vysokou rychlostí ohřevu a snadnou výměnou druhů slitin.Je vhodný pro tavení mědi a slitin mědi s vysokým bodem tání a různých odrůd, jako je bronz a měďnatý nikl.
Vakuová indukční pec je indukční pec vybavená vakuovým systémem, vhodná pro tavení mědi a slitin mědi, které se snadno inhalují a oxidují, jako je bezkyslíkatá měď, beryliový bronz, zirkonový bronz, hořčíkový bronz atd. pro elektrické vakuum.
Tavení v dozvukové peci může rafinovat a odstraňovat nečistoty z taveniny a používá se hlavně při tavení šrotu mědi.Šachtová pec je druh rychlé kontinuální tavicí pece, která má výhody vysoké tepelné účinnosti, vysoké rychlosti tavení a pohodlného vypnutí pece.Lze ovládat;neexistuje žádný proces rafinace, takže velká většina surovin musí být katodová měď.Šachtové pece se obecně používají se stroji pro plynulé lití pro plynulé lití a mohou být také použity s udržovacími pecemi pro polokontinuální lití.
Trend vývoje technologie výroby tavení mědi se odráží především ve snižování ztrát spalováním surovin, snižování oxidace a vdechování taveniny, zlepšování kvality taveniny a přijímání vysoké účinnosti (rychlost tavení indukční pece je vyšší než 10 t/h), velkoobjemové (kapacita indukční pece může být větší než 35 t/soubor), dlouhá životnost (životnost vyzdívky je 1 až 2 roky) a energeticky úsporné (spotřeba energie indukce pec je menší než 360 kW h/t), udržovací pec je vybavena odplyňovacím zařízením (odplyňování CO plynem) a indukční pec Snímač má strukturu spreje, elektrické ovládací zařízení využívá obousměrný tyristor plus zdroj frekvenční konverze, předehřívání pece, monitorování stavu pece a teplotního pole žáruvzdorného a poplašného systému, udržovací pec je vybavena vážícím zařízením a řízení teploty je přesnější.
Výrobní zařízení - Dělicí linka
Výroba linky na dělení měděných pásů je kontinuální linka na dělení a dělení, která rozšiřuje široký svitek přes odvíječ, nařezává svitek na požadovanou šířku přes řezací stroj a převíjí ho na několik svitků přes navíječku.(Skladovací stojan) Pomocí jeřábu uložte role na skladovací regál
↓
(Nakládací vůz) Pomocí podávacího vozíku ručně položte roli materiálu na buben odvíječe a utáhněte jej
↓
(Odvíječ a přítlačný válec proti uvolnění) Rozviňte svitek pomocí otevíracího vedení a přítlačného válečku
↓
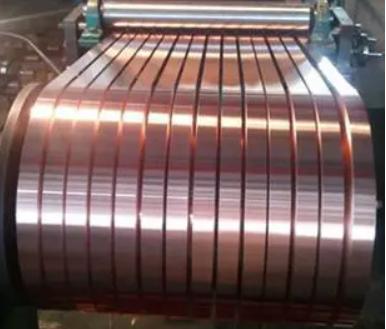
(NO·1 looper a otočný most) úložiště a vyrovnávací paměť
↓
(Zařízení okrajového vodítka a přítlačného válečku) Vertikální válečky vedou list do přítlačných válečků, aby se zabránilo vychýlení, šířka a umístění vertikálního vodícího válečku jsou nastavitelné
↓
(Řezací stroj) vstupte do řezacího stroje pro polohování a řezání
↓
(Rychlovýměnné otočné sedadlo) Výměna skupiny nástrojů
↓
(Zařízení na navíjení šrotu) Odřízněte šrot
↓ (Výstupní vodicí stůl a koncová zarážka cívky) Představte smyčkovač NO.2
↓
(houpací můstek a NO.2 looper) ukládání materiálu a eliminace rozdílu tloušťky
↓
(Zařízení pro napínání lisovací desky a vzduchové expanzní hřídele) zajišťují napínací sílu, oddělení desky a pásu
↓
(Prořezávací nůžky, zařízení na měření délky řízení a vodicí stůl) měření délky, segmentace cívky s pevnou délkou, vodítko navlékání pásky
↓
(navíječka, separační zařízení, tlačné zařízení) separační pás, navíjení
↓
(vykládací vůz, balení) vykládání a balení měděné pásky
Technologie válcování za tepla
Válcování za tepla se používá především pro válcování sochorů ingotů pro výrobu plechů, pásů a fólií.
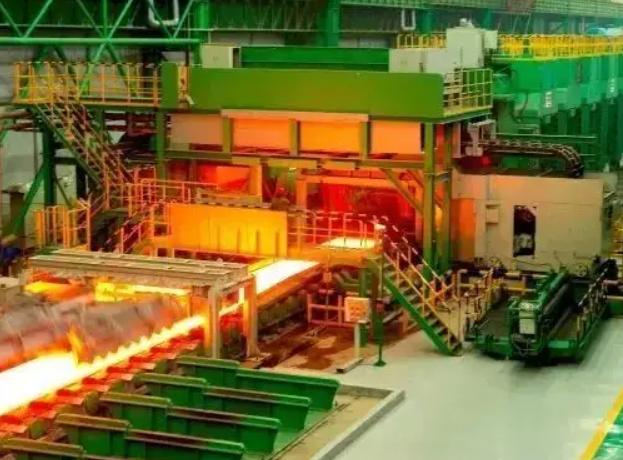
Specifikace ingotů pro válcování předvalků by měly brát v úvahu faktory, jako je rozmanitost produktu, výrobní měřítko, metoda odlévání atd., a souvisí s podmínkami válcovacího zařízení (jako je otvor válce, průměr válce, přípustný válcovací tlak, výkon motoru a délka válečkového stolu) , atd. .Obecně platí, že poměr mezi tloušťkou ingotu a průměrem role je 1: (3,5~7): šířka je obvykle rovna nebo několikanásobku šířky hotového výrobku a šířka a množství ořezu by měly být správně považováno.Obecně by šířka desky měla být 80 % délky těla role.Délka ingotu by měla být přiměřeně uvažována podle výrobních podmínek.Obecně řečeno, za předpokladu, že konečnou teplotu válcování válcování za tepla lze řídit, čím delší je ingot, tím vyšší je efektivita výroby a výtěžnost.
Specifikace ingotů malých a středně velkých závodů na zpracování mědi jsou obecně (60 ~ 150) mm × (220 ~ 450) mm × (2000 ~ 3200) mm a hmotnost ingotu je 1,5 ~ 3 t;specifikace ingotů velkých závodů na zpracování mědi Obecně je to (150–250) mm × (630–1250) mm × (2400–8000) mm a hmotnost ingotu je 4,5–20 t.
Při válcování za tepla teplota povrchu válce prudce stoupá v okamžiku, kdy je válec v kontaktu s vysokoteplotním válcovaným předmětem.Opakovaná tepelná roztažnost a smršťování za studena způsobují praskliny a praskliny na povrchu role.Při válcování za tepla je proto nutné provádět chlazení a mazání.Obvykle se jako chladicí a mazací médium používá voda nebo emulze s nižší koncentrací.Celková pracovní rychlost válcování za tepla je obecně 90 % až 95 %.Tloušťka za tepla válcovaného pásu je obecně 9 až 16 mm.Povrchové frézování pásu po válcování za tepla může odstranit povrchové oxidové vrstvy, intruze okují a další povrchové vady vzniklé během odlévání, ohřevu a válcování za tepla.Podle závažnosti povrchových defektů pásu válcovaného za tepla a potřeb procesu je velikost frézování každé strany 0,25 až 0,5 mm.
Válcovací stolice pro válcování za tepla jsou obecně dvouhorní nebo čtyřhorní reverzní válcovací stolice.Se zvětšováním ingotu a neustálým prodlužováním délky pásu má úroveň řízení a funkce válcovny za tepla trend neustálého zlepšování a zlepšování, jako je použití automatického řízení tloušťky, hydraulické ohýbací válce, přední a zadní vertikální válce, pouze chlazení válců bez chlazení Zařízení pro válcování, řízení koruny TP role (Taper Pis-ton Roll), online kalení (kalení) po válcování, online navíjení a další technologie pro zlepšení rovnoměrnosti struktury a vlastností pásu a získání lepších talíř.
Technologie lití
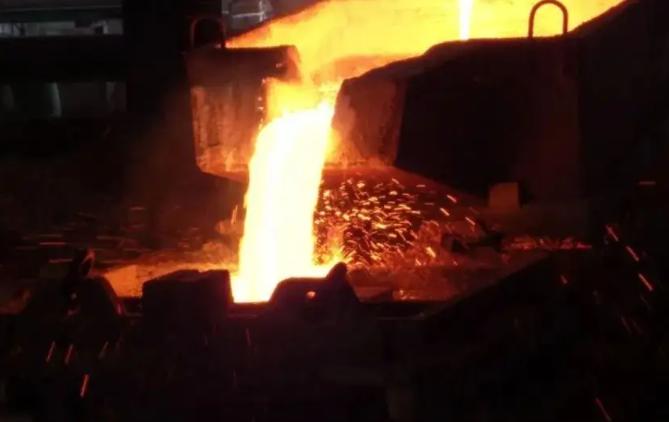
Odlévání mědi a slitin mědi se obecně dělí na: vertikální polokontinuální lití, vertikální plné plynulé lití, horizontální plynulé lití, vzestupné plynulé lití a další technologie lití.
A. Vertikální polokontinuální lití
Vertikální polokontinuální lití má vlastnosti jednoduchého zařízení a flexibilní výroby a je vhodné pro odlévání různých kruhových a plochých ingotů z mědi a slitin mědi.Převodový režim vertikálního polokontinuálního licího stroje je rozdělen na hydraulický, vodící šroub a ocelové lano.Protože je hydraulický převod relativně stabilní, byl více využíván.Krystalizátor lze podle potřeby rozvibrovat s různými amplitudami a frekvencemi.V současné době je metoda polokontinuálního lití široce používána při výrobě ingotů mědi a slitin mědi.
B. Vertikální plné kontinuální lití
Vertikální plné kontinuální lití má vlastnosti velkého výkonu a vysoké výtěžnosti (asi 98 %), je vhodné pro velkosériovou a kontinuální výrobu ingotů s jedinou odrůdou a specifikací a stává se jednou z hlavních výběrových metod pro tavení a odlévání. proces na moderních velkosériových linkách na výrobu měděných pásů.Vertikální plná forma pro plynulé lití využívá bezkontaktní laserové automatické řízení hladiny kapaliny.Licí stroj obecně využívá hydraulické upínání, mechanickou převodovku, online řezání suchých třísek chlazených olejem a sběr třísek, automatické značení a naklánění ingotu.Struktura je složitá a stupeň automatizace je vysoký.
C. Horizontální kontinuální lití
Horizontálním kontinuálním litím lze vyrábět sochory a drátěné sochory.
Pásové horizontální plynulé lití může vyrábět pásy z mědi a slitin mědi o tloušťce 14-20 mm.Pásy v tomto rozsahu tloušťky mohou být přímo válcovány za studena bez válcování za tepla, takže se často používají k výrobě slitin, které se obtížně válcovají za tepla (jako je cín. Fosforový bronz, olověná mosaz atd.), lze vyrábět i mosaz, cupronickel a pásek z nízkolegované slitiny mědi.V závislosti na šířce licího pásu může horizontální plynulé lití odlévat 1 až 4 pásy současně.Běžně používané horizontální stroje pro plynulé odlévání mohou odlévat dva pásy současně, každý o šířce menší než 450 mm, nebo odlévat jeden pás o šířce pásu 650-900 mm.Horizontální pás pro plynulé odlévání obecně využívá proces odlévání tah-stop-reverzní tlak a na povrchu jsou periodické krystalizační linie, které by měly být obecně eliminovány frézováním.Existují domácí příklady měděných pásů s vysokým povrchem, které lze vyrábět tažením a odléváním předvalků pásu bez frézování.
Horizontální plynulé lití předvalků trubek, tyčí a drátů může odlévat 1 až 20 ingotů současně podle různých slitin a specifikací.Obecně je průměr tyčového nebo drátěného polotovaru 6 až 400 mm a vnější průměr trubkového polotovaru je 25 až 300 mm.Tloušťka stěny je 5-50 mm a délka strany ingotu je 20-300 mm.Výhody metody horizontálního kontinuálního lití spočívají v tom, že proces je krátký, výrobní náklady jsou nízké a efektivita výroby je vysoká.Zároveň je to také nezbytný způsob výroby některých slitinových materiálů se špatnou zpracovatelností za tepla.V poslední době je to hlavní způsob výroby předvalků běžně používaných měděných výrobků, jako jsou pásy cín-fosforový bronz, pásy slitiny zinku a niklu a klimatizační trubky z mědi deoxidované fosforem.výrobních metod.
Nevýhody způsobu výroby horizontálního kontinuálního lití jsou: vhodné druhy slitin jsou relativně jednoduché, spotřeba grafitového materiálu ve vnitřním pouzdru formy je poměrně velká a rovnoměrnost krystalické struktury průřezu ingotu není snadné ovládání.Spodní část ingotu se vlivem gravitace, která je blízko vnitřní stěny formy, nepřetržitě ochlazuje a zrna jsou jemnější;horní část je způsobena tvorbou vzduchových mezer a vysokou teplotou taveniny, která způsobuje zpoždění tuhnutí ingotu, což zpomaluje rychlost ochlazování a způsobuje hysterezi tuhnutí ingotu.Krystalická struktura je poměrně hrubá, což je patrné zejména u velkorozměrových ingotů.S ohledem na výše uvedené nedostatky je v současné době vyvíjen způsob odlévání svislým ohybem s předvalkem.Německá společnost použila kontinuální odlévací zařízení s vertikálním ohýbáním k testování odlévání (16-18) mm × 680 mm cínových bronzových pásů, jako jsou DHP a CuSn6, rychlostí 600 mm/min.
D. Kontinuální lití směrem nahoru
Vzestupné plynulé lití je technologie odlévání, která se za posledních 20 až 30 let rychle vyvíjela a je široce používána při výrobě drátěných předvalků pro dráty z lesklého měděného drátu.Využívá princip vakuového sacího lití a využívá technologii stop-pull k realizaci kontinuálního vícehlavého lití.Má vlastnosti jednoduchého zařízení, malé investice, menší ztráty kovů a postupy s nízkým znečištěním životního prostředí.Kontinuální lití směrem vzhůru je obecně vhodné pro výrobu předvalků z červené mědi a bezkyslíkatých měděných drátů.Novým úspěchem vyvinutým v posledních letech je jeho popularizace a aplikace ve velkoprůměrových trubkových polotovarech, mosazi a kupronniklu.V současné době je vyvinuta vzestupná kontilití jednotka s ročním výkonem 5000 t a průměrem větším než Φ100 mm;Byly vyrobeny binární obyčejné mosazné a zinkově bílé drátové předvalky z ternární slitiny mědi a výtěžnost drátových předvalků může dosáhnout více než 90 %.
E. Jiné techniky lití
Technologie kontinuálního lití sochorů je ve vývoji.Překonává defekty, jako jsou stopy po skluzu vytvořené na vnějším povrchu předvalku v důsledku procesu zastavení-tahu kontinuálního lití směrem nahoru, a kvalita povrchu je vynikající.A díky svým téměř směrovým charakteristikám tuhnutí je vnitřní struktura jednotnější a čistší, takže výkon produktu je také lepší.Technologie výroby předvalků z měděného drátu pro plynulé lití pásového typu byla široce používána ve velkých výrobních linkách nad 3 tuny.Plocha průřezu bramy je obecně větší než 2000 mm2 a na ni navazuje průběžná válcovna s vysokou efektivitou výroby.
Elektromagnetické odlévání se v mé zemi zkoušelo již v 70. letech, ale průmyslová výroba nebyla realizována.V posledních letech udělala technologie elektromagnetického odlévání velký pokrok.V současnosti jsou úspěšně odlévány bezkyslíkaté měděné ingoty Φ200 mm s hladkým povrchem.Současně může míchací účinek elektromagnetického pole na taveninu podporovat odsávání a odstraňování strusky a lze získat měď bez kyslíku s obsahem kyslíku nižším než 0,001 %.
Směrem nové technologie odlévání měděné slitiny je zlepšení struktury formy prostřednictvím směrového tuhnutí, rychlého tuhnutí, polotuhého tváření, elektromagnetického míchání, metamorfní úpravy, automatického řízení hladiny kapaliny a dalších technických prostředků podle teorie tuhnutí., zahušťování, čištění a realizovat nepřetržitý provoz a tvarování na blízkém konci.
V dlouhodobém horizontu bude odlévání mědi a slitin mědi koexistencí technologie polokontinuálního lití a technologie plného kontinuálního lití a aplikační podíl technologie kontinuálního lití se bude nadále zvyšovat.
Technologie válcování za studena
Podle specifikace válcovaného pásu a procesu válcování se válcování za studena dělí na předvalování, meziválcování a dokončovací válcování.Proces válcování za studena odlévaného pásu o tloušťce 14 až 16 mm a za tepla válcovaného předvalku o tloušťce asi 5 až 16 mm až 2 až 6 mm se nazývá blokování a proces pokračujícího snižování tloušťky polotovaru. válcovaný kus se nazývá meziválcování.finální válcování za studena pro splnění požadavků hotového výrobku se nazývá dokončovací válcování.
Proces válcování za studena musí řídit redukční systém (celková rychlost zpracování, rychlost zpracování a rychlost zpracování hotového výrobku) podle různých slitin, specifikací válcování a požadavků na výkon hotového výrobku, přiměřeně vybrat a upravit tvar válce a přiměřeně vybrat mazání. metoda a mazivo.Měření a seřizování tahu.
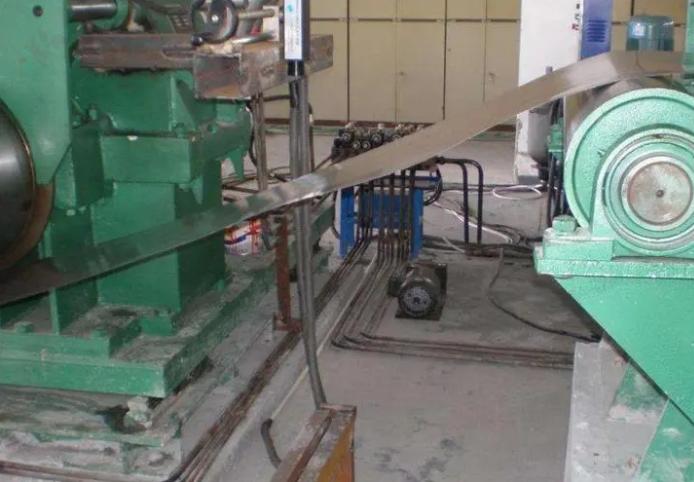
Válcovací stolice pro válcování za studena obecně používají vratné válcovací stolice se čtyřmi vysokými nebo více hlavami.Moderní válcovací stolice pro válcování za studena obecně používají řadu technologií, jako je hydraulické pozitivní a negativní ohýbání válců, automatické řízení tloušťky, tlaku a tahu, axiální pohyb válců, segmentové chlazení válců, automatické řízení tvaru plechu a automatické vyrovnávání válcovaných kusů , takže lze zlepšit přesnost proužku.Až 0,25±0,005 mm a v rámci 5I tvaru desky.
Vývojový trend technologie válcování za studena se odráží ve vývoji a aplikaci vysoce přesných víceválcových stolic, vyšších rychlostí válcování, přesnější kontroly tloušťky a tvaru pásu a pomocných technologií, jako je chlazení, mazání, navíjení, centrování a rychlé válcování. změna.upřesnění atd.
Výrobní zařízení-Zvonová pec
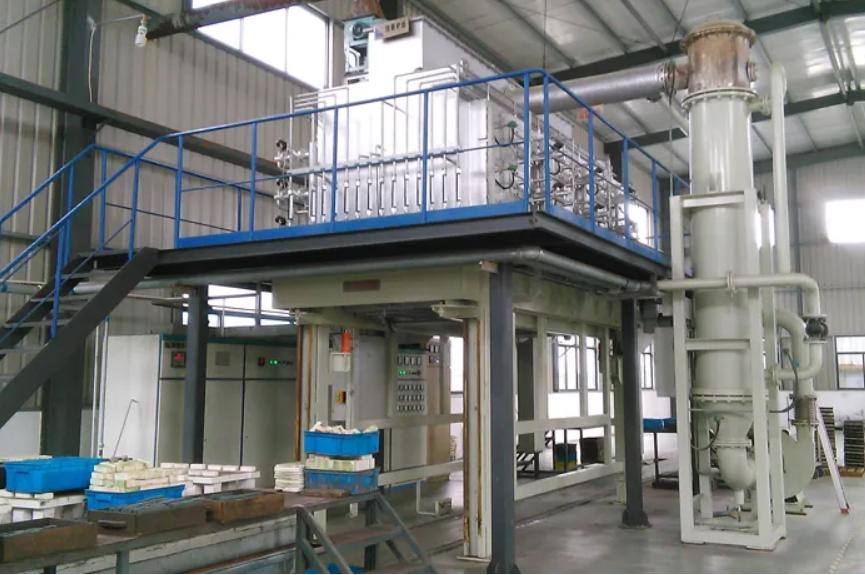
Zvonové pece a zvedací pece se obecně používají v průmyslové výrobě a pilotních testech.Obecně platí, že výkon je velký a spotřeba energie je velká.Pro průmyslové podniky je materiálem pece zvedací pece Luoyang Sigma keramické vlákno, které má dobrý účinek na úsporu energie, nízkou spotřebu energie a nízkou spotřebu energie.Ušetřete elektřinu a čas, což je výhodné pro zvýšení výroby.
Před 25 lety německé BRANDS a Philips, přední společnost v průmyslu výroby feritu, společně vyvinuly nový slinovací stroj.Vývoj tohoto zařízení vychází vstříc speciálním potřebám feritového průmyslu.Během tohoto procesu je zvonová pec BRANDS průběžně aktualizována.
Dbá na potřeby světově uznávaných firem jako Philips, Siemens, TDK, FDK aj., které rovněž velmi těží z kvalitního vybavení BRANDS.
Díky vysoké stabilitě výrobků vyráběných zvonovými pecemi se zvonové pece staly špičkovými společnostmi v profesionálním průmyslu výroby feritu.Před 25 lety první pec vyrobená společností BRANDS stále vyrábí vysoce kvalitní produkty pro Philips.
Hlavní charakteristikou slinovací pece nabízené zvonovou pecí je její vysoká účinnost.Jeho inteligentní řídicí systém a další vybavení tvoří kompletní funkční celek, který dokáže plně vyhovět téměř nejmodernějším požadavkům feritového průmyslu.
Zákazníci se zvonovými pecemi mohou naprogramovat a uložit jakýkoli teplotní/atmosférický profil potřebný k výrobě vysoce kvalitních produktů.Kromě toho mohou zákazníci také vyrábět jakékoli další produkty včas podle skutečných potřeb, čímž zkracují dodací lhůty a snižují náklady.Slinovací zařízení musí mít dobrou nastavitelnost, aby bylo možné vyrábět řadu různých produktů, aby se neustále přizpůsobovaly potřebám trhu.To znamená, že odpovídající produkty musí být vyráběny podle potřeb jednotlivých zákazníků.
Dobrý výrobce feritů může vyrobit více než 1000 různých magnetů, aby vyhověl speciálním potřebám zákazníků.Ty vyžadují schopnost opakovat proces slinování s vysokou přesností.Systémy zvonových pecí se staly standardními pecemi pro všechny výrobce feritu.
Ve feritovém průmyslu se tyto pece používají hlavně pro nízkou spotřebu energie a ferit s vysokou hodnotou μ, zejména v komunikačním průmyslu.Bez zvonové pece není možné vyrábět vysoce kvalitní jádra.
Zvonová pec vyžaduje během spékání pouze několik operátorů, nakládání a vykládání lze dokončit během dne a spékání lze dokončit v noci, což umožňuje špičkové oholení elektřiny, což je v dnešní situaci nedostatku energie velmi praktické.Zvonové pece produkují vysoce kvalitní výrobky a všechny dodatečné investice se díky vysoce kvalitním výrobkům rychle vrátí.Regulace teploty a atmosféry, design pece a regulace proudění vzduchu v peci jsou dokonale integrovány pro zajištění rovnoměrného ohřevu a chlazení produktu.Řízení atmosféry pece během chlazení přímo souvisí s teplotou pece a může zaručit obsah kyslíku 0,005 % nebo dokonce nižší.A to jsou věci, které naši konkurenti neumí.
Díky kompletnímu alfanumerickému programovacímu vstupnímu systému lze dlouhé slinovací procesy snadno replikovat a zajistit tak kvalitu produktu.Při prodeji produktu je to také odraz kvality produktu.
Technologie tepelného zpracování
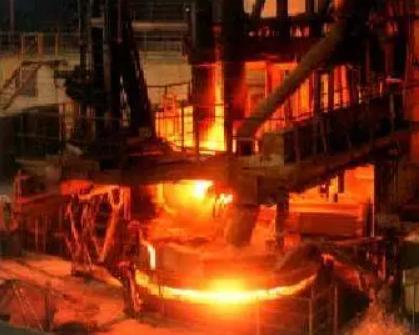
Několik slitinových ingotů (pásů) se silnou segregací dendritu nebo namáháním odléváním, jako je cín-fosforový bronz, musí projít speciálním homogenizačním žíháním, které se obvykle provádí ve zvonové peci.Teplota homogenizačního žíhání je obecně mezi 600 a 750 °C.
V současné době je většina mezižíhání (rekrystalizační žíhání) a dokončeného žíhání (žíhání pro kontrolu stavu a výkonu výrobku) pásů měděných slitin leskle žíhána ochranou plynem.Mezi typy pecí patří zvonová pec, pec se vzduchovým polštářem, vertikální trakční pec atd. Oxidační žíhání se postupně vyřazuje.
Trend vývoje technologie tepelného zpracování se promítá do válcování za tepla on-line roztokového zpracování precipitací zpevněných slitinových materiálů a následné technologie deformačního tepelného zpracování, kontinuálního lesklého žíhání a tahového žíhání v ochranné atmosféře.
Kalení – tepelné zpracování stárnutím se používá hlavně pro tepelně zpracovatelné zpevnění slitin mědi.Tepelným zpracováním výrobek mění svou mikrostrukturu a získává požadované speciální vlastnosti.S vývojem vysoce pevných a vysoce vodivých slitin se bude více uplatňovat proces tepelného zpracování kalením a stárnutím.Zařízení pro úpravu stárnutím je zhruba stejné jako zařízení pro žíhání.
Technologie vytlačování
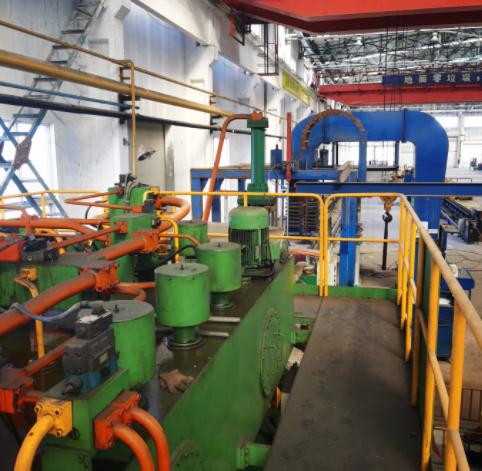
Extruze je vyzrálá a pokročilá metoda výroby trubek, tyčí, profilů a polotovarů z mědi a slitin mědi.Změnou matrice nebo použitím metody perforačního vytlačování lze přímo vytlačovat různé druhy slitin a různé tvary průřezu.Prostřednictvím vytlačování se odlévaná struktura ingotu změní na zpracovanou strukturu a vytlačovaný předvalek z trubek a předvalek z tyče mají vysokou rozměrovou přesnost a struktura je jemná a jednotná.Metoda vytlačování je výrobní metoda běžně používaná domácími i zahraničními výrobci měděných trubek a tyčí.
Kování slitin mědi provádějí hlavně výrobci strojů v mé zemi, zejména včetně volného kování a zápustkového kování, jako jsou velká ozubená kola, šneková kola, šneky, ozubené kroužky automobilových synchronizátorů atd.
Metodu vytlačování lze rozdělit do tří typů: dopředná extruze, zpětná extruze a speciální extruze.Mezi nimi existuje mnoho aplikací dopředného vytlačování, zpětné vytlačování se používá při výrobě tyčí a drátů malých a středních rozměrů a speciální vytlačování se používá ve speciální výrobě.
Při vytlačování by měl být podle vlastností slitiny, technických požadavků vytlačovaných výrobků a kapacity a struktury vytlačovacího stroje rozumně zvolen typ, velikost a koeficient vytlačování ingotu tak, aby stupeň deformace byl ne méně než 85 %.Teplota vytlačování a rychlost vytlačování jsou základní parametry procesu vytlačování a přiměřený rozsah teplot vytlačování by měl být určen podle diagramu plasticity a fázového diagramu kovu.U mědi a slitin mědi je teplota vytlačování obecně mezi 570 a 950 °C a teplota vytlačování z mědi je dokonce až 1000 až 1050 °C.Ve srovnání s teplotou ohřevu vytlačovacího válce 400 až 450 °C je teplotní rozdíl mezi těmito dvěma poměrně vysoký.Pokud je rychlost vytlačování příliš nízká, teplota povrchu ingotu bude klesat příliš rychle, což má za následek zvýšení nerovnoměrnosti toku kovu, což povede ke zvýšení zatížení vytlačováním a dokonce způsobí nudný jev. .Proto měď a slitiny mědi obecně používají relativně vysokorychlostní vytlačování, rychlost vytlačování může dosáhnout více než 50 mm/s.
Při vytlačování mědi a slitin mědi se k odstranění povrchových vad ingotu často používá odlupovací vytlačování a odlupovací tloušťka je 1-2 m.Vodní těsnění se obecně používá na výstupu z vytlačovacího předvalku, takže produkt může být ochlazen ve vodní nádrži po vytlačování a povrch produktu není oxidován a následné zpracování za studena může být prováděno bez moření.Má tendenci používat velkotonážní extrudér se synchronním navíjecím zařízením k vytlačování trubkových nebo drátěných svitků s jednou hmotností větší než 500 kg, aby se efektivně zlepšila efektivita výroby a komplexní výtěžek následné sekvence.V současné době se při výrobě trubek z mědi a slitin mědi používá převážně horizontální hydraulické dopředné extrudéry s nezávislým perforačním systémem (dvojčinný) a přímým převodem olejového čerpadla a výroba tyčí většinou využívá nesamostatný perforační systém (jednočinný) a olejové čerpadlo přímý převod.Horizontální hydraulický vytlačovací stroj vpřed nebo vzad.Běžně používané specifikace extruderu jsou 8-50 MN a nyní mají tendenci být vyráběny velkotonážními extrudéry nad 40 MN, aby se zvýšila jednotlivá hmotnost ingotu, čímž se zlepšila efektivita výroby a výtěžnost.
Moderní horizontální hydraulické extrudery jsou konstrukčně vybaveny předpjatým integrálním rámem, vytlačovacím válcem "X" vedením a podpěrou, vestavěným perforačním systémem, vnitřním chlazením perforační jehly, posuvnou nebo rotační sadou matric a zařízením pro rychlou výměnu matrice, vysoce výkonným variabilním přímým olejovým čerpadlem pohon, integrovaný logický ventil, řízení PLC a další pokročilé technologie, zařízení má vysokou přesnost, kompaktní strukturu, stabilní provoz, bezpečné blokování a snadno realizovatelné ovládání programu.Technologie kontinuálního vytlačování (Conform) zaznamenala v posledních deseti letech určitý pokrok, zejména pro výrobu tyčí speciálního tvaru, jako jsou dráty pro elektrické lokomotivy, což je velmi perspektivní.V posledních desetiletích se rychle vyvíjela nová technologie vytlačování a vývojový trend technologie vytlačování je ztělesněn následovně: (1) Vytlačovací zařízení.Vytlačovací síla vytlačovacího lisu se bude vyvíjet větším směrem a vytlačovací lis o více než 30 MN se stane hlavním tělem a automatizace výrobní linky vytlačovacích lisů se bude nadále zlepšovat.Moderní vytlačovací stroje zcela přijaly řízení počítačovým programem a programovatelné logické řízení, takže se výrazně zlepšila efektivita výroby, výrazně se snížila obsluha a dokonce je možné realizovat automatický bezobslužný provoz vytlačovacích výrobních linek.
Struktura těla extrudéru byla také neustále vylepšována a zdokonalována.V posledních letech některé horizontální extrudéry přijaly předpjatý rám, aby byla zajištěna stabilita celkové konstrukce.Moderní extruder realizuje metody přímého a zpětného vytlačování.Extrudér je vybaven dvěma vytlačovacími hřídeli (hlavní vytlačovací hřídel a hřídel matrice).Během vytlačování se vytlačovací válec pohybuje s hlavním hřídelem.V tomto okamžiku je produktem. Směr výtoku je konzistentní se směrem pohybu hlavního hřídele a opačný k relativnímu směru pohybu osy lisovnice.Základna extrudéru také přijímá konfiguraci více stanic, což nejen usnadňuje výměnu formy, ale také zlepšuje efektivitu výroby.Moderní extrudéry používají zařízení pro regulaci laserové odchylky, které poskytuje efektivní údaje o stavu středové linie vytlačování, což je vhodné pro včasné a rychlé nastavení.Hydraulický lis s přímým pohonem vysokotlakého čerpadla využívající jako pracovní médium olej zcela nahradil hydraulický lis.Vytlačovací nástroje jsou také neustále aktualizovány s vývojem technologie vytlačování.Vnitřní propichovací jehla chlazená vodou byla široce propagována a propichovací a válcovací jehla s proměnným průřezem výrazně zlepšuje mazací účinek.Širší využití mají keramické formy a formy z legované oceli s delší životností a vyšší kvalitou povrchu.
Vytlačovací nástroje jsou také neustále aktualizovány s vývojem technologie vytlačování.Vnitřní propichovací jehla chlazená vodou byla široce propagována a propichovací a válcovací jehla s proměnným průřezem výrazně zlepšuje mazací účinek.Více oblíbená je aplikace keramických forem a forem z legované oceli s delší životností a vyšší kvalitou povrchu.(2) Proces výroby vytlačování.Odrůdy a specifikace extrudovaných výrobků se neustále rozšiřují.Extruze malých průřezů, ultra vysoce přesných trubek, tyčí, profilů a supervelkých profilů zajišťuje kvalitu vzhledu výrobků, snižuje vnitřní vady výrobků, snižuje geometrické ztráty a dále podporuje metody extruze, jako je rovnoměrný výkon extrudovaných produkty.Moderní technologie zpětného vytlačování je také široce používána.Pro snadno oxidovatelné kovy se používá vytlačování vodního těsnění, které může snížit znečištění mořením, snížit ztráty kovu a zlepšit kvalitu povrchu výrobků.U extrudovaných produktů, které je třeba zchladit, stačí řídit vhodnou teplotu.Metoda vytlačování vodního těsnění může dosáhnout účelu, efektivně zkrátit výrobní cyklus a ušetřit energii.
S neustálým zlepšováním kapacity extruderu a technologie extruze se postupně uplatňovala moderní technologie extruze, jako je izotermická extruze, extruze chladicí matrice, vysokorychlostní extruze a další technologie dopředné extruze, zpětná extruze, hydrostatická extruze Praktická aplikace technologie kontinuální extruze lisování a Conform, aplikace technologie vytlačování prášku a vrstveného kompozitního vytlačování nízkoteplotních supravodivých materiálů, vývoj nových metod, jako je vytlačování polotuhých kovů a vytlačování více polotovarů, vývoj malých přesných dílů Technologie tváření vytlačováním za studena, atd., byly rychle vyvinuty a široce vyvinuty a používány.
Spektrometr
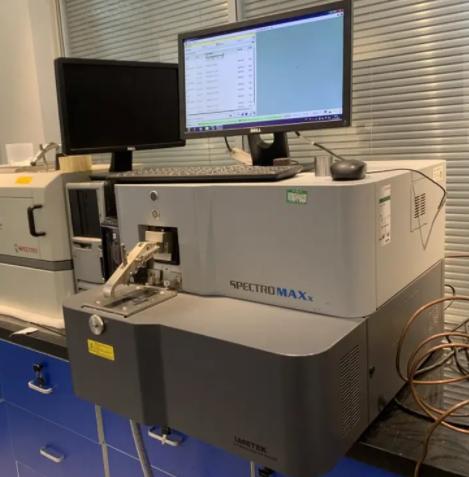
Spektroskop je vědecký přístroj, který rozkládá světlo složitého složení na spektrální čáry.Sedmibarevné světlo ve slunečním světle je část, kterou dokáže rozeznat pouhým okem (viditelné světlo), ale pokud je sluneční světlo rozloženo spektrometrem a uspořádáno podle vlnové délky, viditelné světlo zaujímá pouze malý rozsah spektra a zbytek je spektra, která nelze rozlišit pouhým okem, jako jsou infračervené paprsky, mikrovlny, UV paprsky, rentgenové paprsky atd. Optické informace jsou zachyceny spektrometrem, vyvolány fotografickým filmem nebo zobrazeny a analyzovány na počítačovém automatickém displeji numerický přístroj, aby bylo možné zjistit, jaké prvky jsou v předmětu obsaženy.Tato technologie je široce používána při detekci znečištění ovzduší, znečištění vody, hygieny potravin, kovoprůmyslu atd.
Spektrometr, také známý jako spektrometr, je široce známý jako spektrometr s přímým čtením.Zařízení, které měří intenzitu spektrálních čar na různých vlnových délkách pomocí fotodetektorů, jako jsou fotonásobiče.Skládá se ze vstupní štěrbiny, disperzního systému, zobrazovacího systému a jedné nebo více výstupních štěrbin.Elektromagnetické záření zdroje záření je disperzním prvkem rozděleno do požadované vlnové délky nebo oblasti vlnových délek a intenzita je měřena na zvolené vlnové délce (nebo skenování určitého pásma).Existují dva typy monochromátorů a polychromátorů.
Testovací přístroj-měřič vodivosti
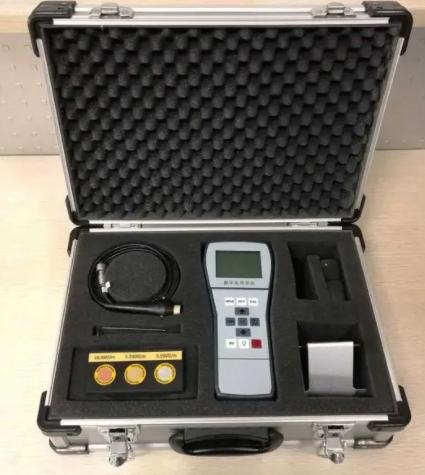
Digitální ruční zkoušečka vodivosti kovu (měřič vodivosti) FD-101 využívá princip detekce vířivých proudů a je speciálně navržena podle požadavků elektrotechnického průmyslu na vodivost.Z hlediska funkce a přesnosti splňuje zkušební normy kovoprůmyslu.
1. Měřič vodivosti vířivých proudů FD-101 má tři jedinečné:
1) Jediný čínský měřič vodivosti, který prošel ověřením Ústavu leteckých materiálů;
2) Jediný čínský měřič vodivosti, který dokáže vyhovět potřebám společností v leteckém průmyslu;
3) Jediný čínský měřič vodivosti exportovaný do mnoha zemí.
2. Představení funkce produktu:
1) Velký rozsah měření: 6,9%IACS-110%IACS(4,0MS/m-64MS/m), který splňuje test vodivosti všech neželezných kovů.
2) Inteligentní kalibrace: rychlá a přesná, zcela se vyhne chybám ruční kalibrace.
3) Přístroj má dobrou teplotní kompenzaci: odečet je automaticky kompenzován na hodnotu při 20 °C a korekce není ovlivněna lidskou chybou.
4) Dobrá stabilita: je to váš osobní strážce pro kontrolu kvality.
5) Humanizovaný inteligentní software: Přináší vám pohodlné detekční rozhraní a výkonné funkce pro zpracování a sběr dat.
6) Pohodlný provoz: místo výroby a laboratoř lze využít všude a získat si přízeň většiny uživatelů.
7) Vlastní výměna sond: Každý hostitel může být vybaven více sondami a uživatelé je mohou kdykoli vyměnit.
8) Číselné rozlišení: 0,1 % IACS (MS/m)
9) Měřicí rozhraní současně zobrazuje naměřené hodnoty ve dvou jednotkách %IACS a MS/m.
10) Má funkci uchovávání naměřených dat.
Tvrdoměr
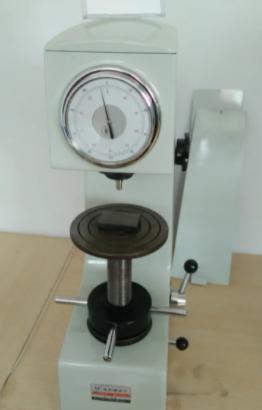
Přístroj má jedinečný a přesný design v oblasti mechaniky, optiky a světelného zdroje, díky čemuž je zobrazení vtisku jasnější a měření přesnější.Měření se mohou účastnit objektivy 20x i 40x, díky čemuž je rozsah měření větší a aplikace rozsáhlejší.Přístroj je vybaven digitálním měřicím mikroskopem, který může na sítu kapaliny zobrazit zkušební metodu, zkušební sílu, délku vtisku, hodnotu tvrdosti, dobu držení zkušební síly, časy měření atd., a má závitové rozhraní, které lze připojit na digitální fotoaparát a CCD kameru.V domácích hlavových výrobcích má určitou reprezentativnost.
Testovací přístrojový detektor odporu
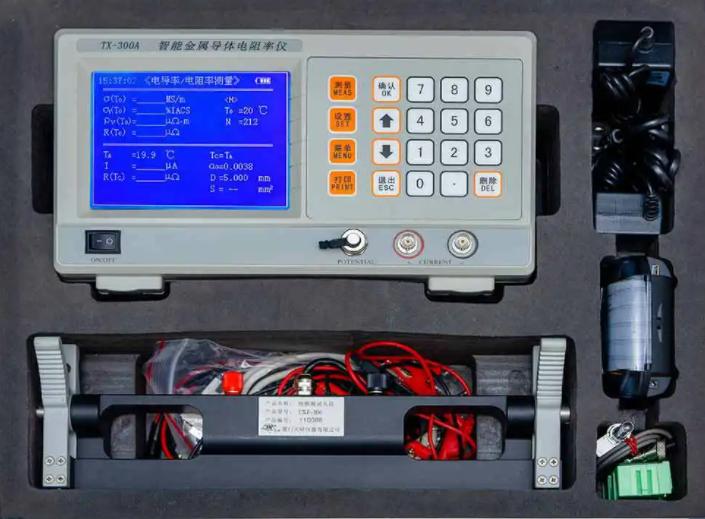
Měřicí přístroj odporu kovového drátu je vysoce výkonný testovací přístroj pro parametry, jako je odpor drátu, tyče a elektrická vodivost.Jeho výkon plně odpovídá příslušným technickým požadavkům v GB/T3048.2 a GB/T3048.4.Široce se používá v metalurgii, elektrické energii, drátech a kabelech, elektrických spotřebičích, vysokých školách a univerzitách, vědeckých výzkumných jednotkách a dalších průmyslových odvětvích.
Hlavní vlastnosti nástroje:
(1) Integruje pokročilou elektronickou technologii, jednočipovou technologii a technologii automatické detekce se silnou automatizační funkcí a jednoduchým ovládáním;
(2) Stačí stisknout tlačítko jednou, všechny naměřené hodnoty lze získat bez jakéhokoli výpočtu, vhodné pro nepřetržitou, rychlou a přesnou detekci;
(3) Bateriový design, malá velikost, snadno se přenáší, vhodný pro použití v terénu a v terénu;
(4) Velká obrazovka, velké písmo, může zobrazovat odpor, vodivost, odpor a další naměřené hodnoty a teplotu, testovací proud, koeficient teplotní kompenzace a další pomocné parametry současně, velmi intuitivní;
(5) Jeden stroj je víceúčelový se 3 měřicími rozhraními, jmenovitě rozhraním pro měření odporu a vodivosti vodičů, rozhraním pro komplexní měření parametrů kabelu a rozhraním pro měření stejnosměrného odporu kabelu (typ TX-300B);
(6) Každé měření má funkce automatického výběru konstantního proudu, automatické komutace proudu, automatické korekce nulového bodu a automatické korekce kompenzace teploty, aby byla zajištěna přesnost každé hodnoty měření;
(7) Jedinečný přenosný čtyřsvorkový testovací přípravek je vhodný pro rychlé měření různých materiálů a různých specifikací drátů nebo tyčí;
(8) Vestavěná datová paměť, která může zaznamenat a uložit 1000 sad naměřených dat a parametrů měření a připojit se k hornímu počítači pro vytvoření kompletní zprávy.